Everything about corrective maintenance in industry
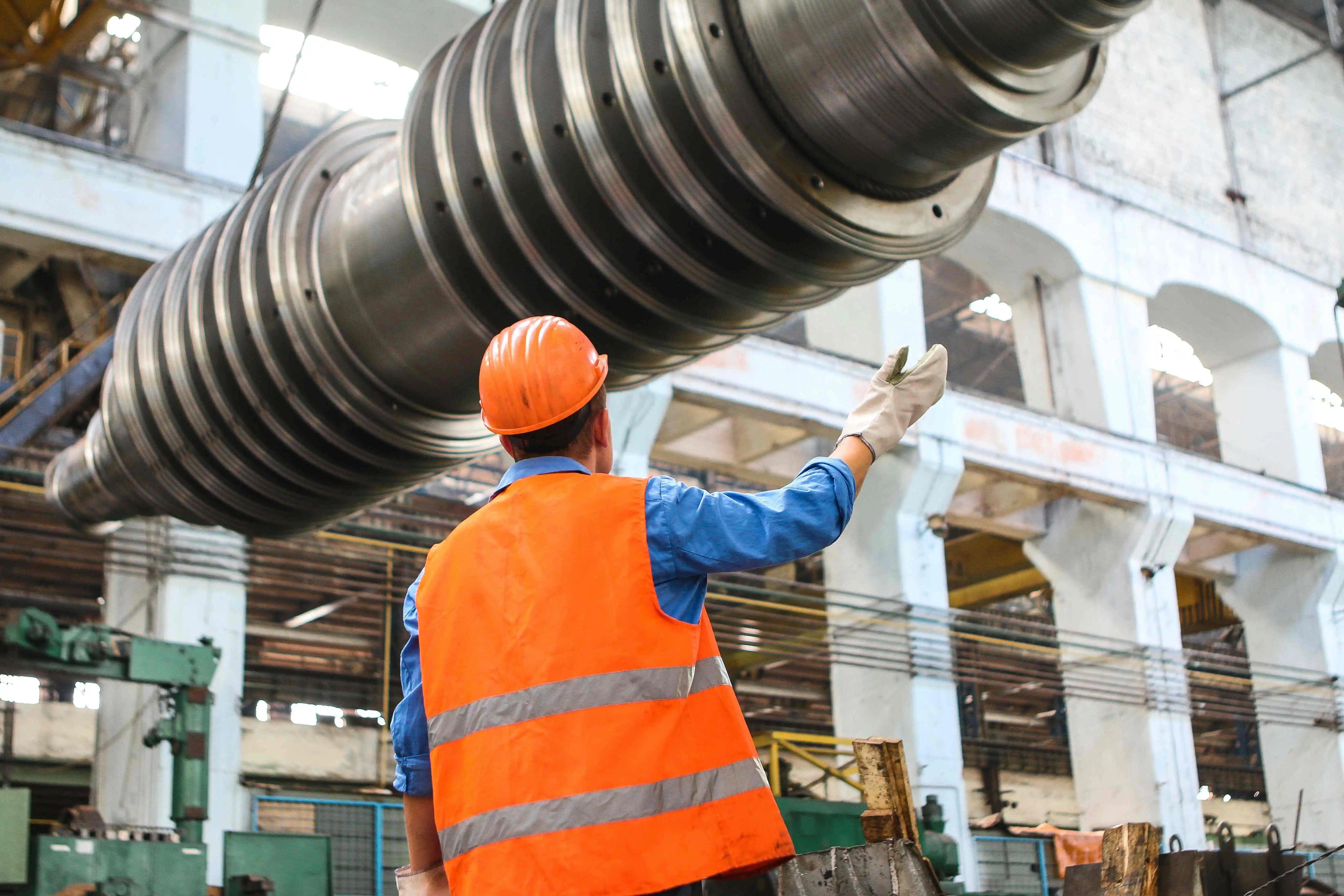
The corrective maintenance allows companies to minimize unplanned downtime and optimize their operational efficiency. But how can it be effectively implemented? And what are the differences compared to other types of maintenance? We’ll explain it all to you.
- What are the 5 types of maintenance?
- Corrective Maintenance: Definition
- Why is corrective maintenance important?
- Steps of corrective maintenance
- Tools and technologies for corrective maintenance
- How to choose your corrective maintenance tool
What are the 5 types of maintenance?
Maintenance encompasses actions and processes aimed at ensuring the sustainability, reliability, and proper functioning of:
- Equipment
- Infrastructure
- or Systems
It also helps prevent breakdowns while repairing failures.
The main objective of maintenance is to optimize the lifespan of industrial assets, reduce operating costs, and minimize unplanned interruptions in operations.
There are 5 types of maintenance:
- Corrective Maintenance: This form of corrective maintenance intervenes after a breakdown or malfunction has occurred.
- Predictive Maintenance: Predictive maintenance relies on the use of data and advanced technologies to monitor the real-time status of equipment.
- Conditional Maintenance: Conditional maintenance is based on continuous monitoring of specific parameters, such as temperature, pressure, or vibrations.
- Repair Maintenance: Lastly, repair maintenance involves restoring equipment to working condition after it has been removed from production due to its age or obsolescence.
Each of these maintenance types has its advantages and disadvantages, and the choice of strategy will depend on your company’s specific needs. In this article, we’ll focus on corrective maintenance, which we’ll present now.
Corrective Maintenance: Definition
What is a corrective intervention?
A corrective intervention, as the name suggests, responds to equipment breakdowns or failures. Its main objective is to quickly and effectively restore the functionality and performance of the equipment. This form of maintenance is generally performed after signs of malfunction or breakdown have been detected.
Corrective maintenance is often considered reactive. It reacts to problems after they have occurred. While it’s an essential element of maintenance management, relying solely on corrective maintenance can lead to unplanned downtime and high repair costs. That’s why it’s important to complement it with other forms of maintenance, particularly preventive maintenance.
What’s the difference between corrective and preventive?
The main difference between corrective and preventive maintenance lies in the timing of actions taken. Corrective maintenance acts after a breakdown has occurred, whereas preventive maintenance aims to prevent breakdowns before they occur.
Preventive maintenance involves regular inspections, tests, and minor repair work to identify and address potential issues before they turn into costly breakdowns. It relies on planning and anticipating maintenance needs, minimizing unplanned downtime and extending the lifespan of equipment.
While preventive maintenance is more proactive, corrective maintenance is necessary to address unforeseen circumstances.
Why is corrective maintenance important?
- Responsiveness to breakdowns
The primary reason why corrective maintenance is important lies in its ability to react quickly to breakdowns. It minimizes the downtime of your equipment and processes, ensuring seamless operational continuity.
- Preservation of investments
Corrective maintenance can contribute to extending the lifespan of your assets, resulting in long-term savings. By intervening at the first signs of malfunction, you avoid more costly repairs or complete equipment replacement.
- Operational safety
The safety of your employees and customers is a priority. Corrective maintenance ensures that your facilities and equipment are in proper working order, reducing the risks of accidents due to equipment failures.
- Maintenance of quality
The quality of your products or services is closely tied to the performance of your equipment. By practicing corrective maintenance, you ensure that your production maintains high quality, thereby enhancing customer satisfaction.
- Time and cost savings
Regular maintenance, even if it doesn’t seem urgent, saves you time and money in the long run. Avoiding costly repairs and unexpected interruptions in your operations can make a significant financial difference.
- Enhancement of reputation
By keeping your equipment in perfect working order, you demonstrate your commitment to quality and reliability, which can strengthen your company’s reputation. Customers tend to trust companies that take care of their equipment.
- Regulatory compliance
In many sectors, corrective maintenance is essential for complying with regulations. Neglecting this practice could expose you to penalties and litigation.
To optimize your logistics management, equip yourself with the best market solutions!
Steps of corrective maintenance
- Identification of the breakdown
The first step of corrective maintenance is to identify the breakdown or failure. It’s essential to precisely diagnose the problem to determine the nature of the necessary intervention. This step relies on careful observation and analysis of failure symptoms.
- Root cause isolation
Once the breakdown is identified, the next step is to determine the root cause of the problem. Understanding what caused the failure is crucial to prevent its recurrence in the future. This often requires thorough testing and investigations to pinpoint the source of the malfunction.
- Intervention planning
Corrective maintenance cannot be improvised. Precise planning is necessary to minimize downtime and costs. This phase involves defining the necessary resources, establishing an intervention schedule, and coordinating technical teams.
- Repair or replacement
Once the root cause is identified and the intervention plan is in place, it’s time to proceed with the repair or replacement of faulty components. This step can vary significantly depending on the nature of the failure, ranging from simple repairs to complete replacements.
- Verification and testing
After the repairs are completed, it’s essential to perform verifications and tests to ensure that the equipment or system is functioning correctly. This phase ensures that corrective maintenance has achieved its goal of restoring functionality.
- Follow-up and evaluation
After corrective maintenance, it’s essential to monitor the equipment or system to ensure that it continues to operate optimally. Evaluating the results of the intervention allows adjustments to future maintenance procedures and optimization of asset durability.
Tools and technologies for corrective maintenance
- Diagnostic tools
The first step of corrective maintenance involves diagnosing the breakdown or malfunction. To do this, technicians can use various diagnostic tools such as multimeters, oscilloscopes, thermal cameras, or specific diagnostic software. These tools enable the rapid identification of the problem, crucial for minimizing downtime.
- Computerized Maintenance Management System (CMMS) software
CMMS software is designed to plan, organize, and track maintenance activities. They manage equipment, anticipate breakdowns, optimize spare part management, and track intervention history. CMMS facilitates the coordination of maintenance teams and contributes to more efficient corrective maintenance.
- Remote monitoring technologies
Remote monitoring of equipment, using sensors and telemetry systems, has become common practice in corrective maintenance. These technologies detect anomalies in real-time, allowing for quick intervention before a major breakdown occurs. Remote monitoring improves the responsiveness of maintenance teams and reduces costs associated with unplanned shutdowns.
- 3D printers
3D printers have become valuable tools in corrective maintenance, especially for manufacturing custom spare parts. In case of unavailable spare parts on the market, 3D printers can be used to create specific components, reducing downtime.
How to choose your corrective maintenance tool
- Evaluate your specific needs
Before searching for the ideal corrective maintenance tool, clearly identify your company’s needs. Ask yourself questions such as: What equipment needs maintenance? What is the expected workload volume? What types of interventions need to be performed? This initial step is crucial to define the functionalities you actually need.
- Compatibility with existing systems
Ensure that the corrective maintenance tool you’re considering is compatible with your existing systems. It should seamlessly integrate into your current technological infrastructure, minimizing potential disruptions.
- Real-time tracking and reporting
The tool should allow real-time tracking of corrective maintenance activities. Make sure it offers advanced reporting features, enabling you to track performance, costs, and make informed decisions.
- Technical support and training
Technical support is essential. Ensure that the tool provider offers quality assistance and adequate training to ensure optimal tool usage.
- Total cost of ownership
Carefully examine the costs associated with the corrective maintenance tool. Consider acquisition, implementation, operational, and long-term maintenance costs. Establish a realistic budget to avoid financial surprises.
- Evaluate user experiences
Look for user experiences and testimonials from other companies using the tool you’re considering. This will give you insights into how it performs in similar contexts.